Table of Contents
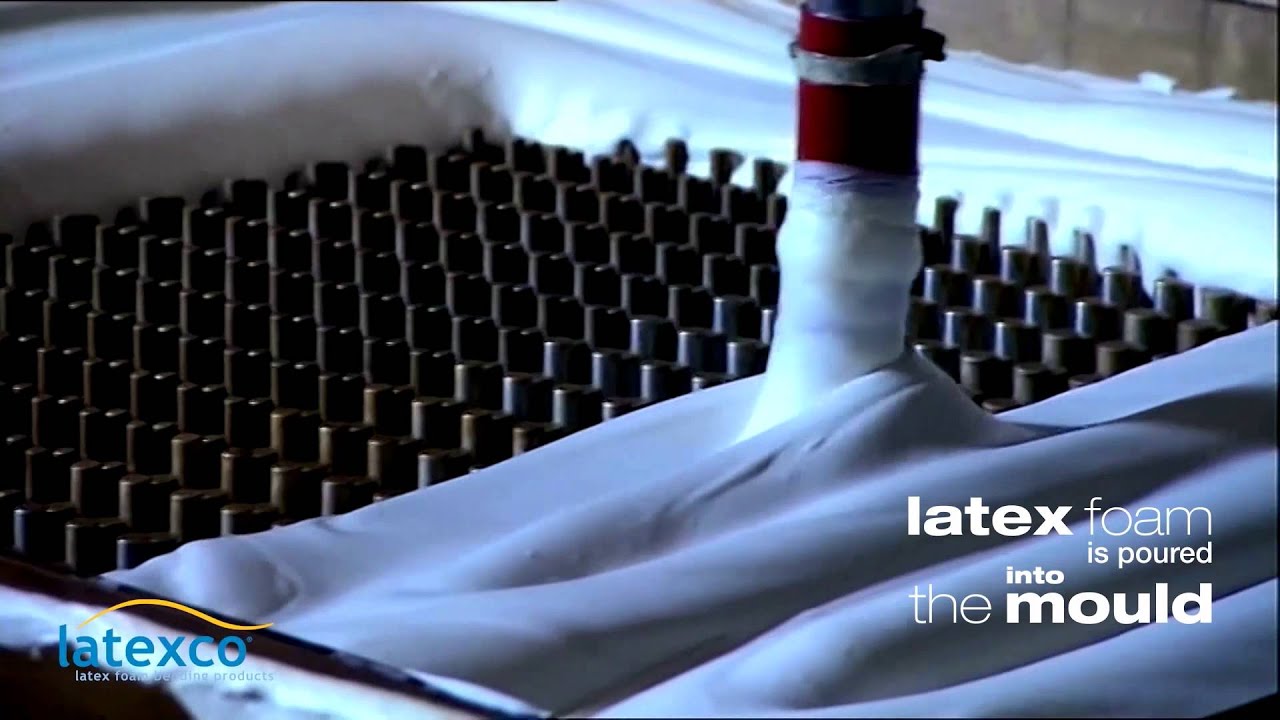
What is latex made of? The primary ingredient in latex foam is the sap of the rubber tree. This video shows how the tree sap is harvested, collected, poured into a mold, and cured at a high temperature. The result is a durable, pressure-relieving foam material free of toxic chemicals and will not emanate any toxic VOCs.
Introduction
Overview of Dunlop Natural latex
Dunlop natural latex is a high-quality, eco-friendly material derived from the sap of the Hevea brasiliensis, commonly known as the rubber tree. Known for its remarkable durability, support, and pressure relief properties, Dunlop latex has become a popular choice for bedding products, particularly mattresses. The manufacturing process of Dunlop natural latex involves a series of steps that transform the raw sap from rubber trees into a comfortable and supportive foam layer, which is then integrated into various mattresses.
Importance of GOLS certification for latex mattresses
The Global Organic Latex Standard (GOLS) is a prestigious certification that ensures the latex used in mattresses is produced environmentally friendly and socially responsible. This certification guarantees that the materials and processes used in manufacturing latex mattresses meet strict criteria regarding organic content, sustainability, and ethical labor practices. Consumers who purchase GOLS-certified latex mattresses can trust that they are investing in a high-quality, eco-conscious product that supports the well-being of both people and the planet.
Role of Dunlop latex foam layer in GOLS-certified latex mattresses
In GOLS-certified latex mattresses, the Dunlop latex foam layer provides the desired comfort, support, and durability. The unique properties of Dunlop natural latex, such as its responsiveness and temperature regulation, make it an ideal material for mattresses. Additionally, its hypoallergenic and eco-friendly qualities further contribute to the overall appeal of GOLS-certified latex mattresses. By understanding the manufacturing process of Dunlop natural latex from rubber tree plantation to the finished foam layer, consumers can appreciate the commitment to quality, sustainability, and innovation that goes into creating these exceptional sleep products.
Uses for latex sap from the rubber tree (Hevea Brasiliensis)
- Rubber products: The primary use of natural latex is in producing rubber products such as tires, hoses, belts, and gaskets. It is valued for its elasticity, durability, and resistance to abrasion and tearing.
- Gloves: Latex gloves are commonly used in medical, dental, and laboratory settings for their flexibility, tactile sensitivity, and barrier protection properties.
- Condoms: Natural latex is widely used to make condoms due to its elasticity, strength, and ability to act as a barrier against sexually transmitted infections (STIs) and unintended pregnancies.
- Balloons: Latex balloons are popular for decorations and celebrations, as the material is stretchable, durable, and can hold gas for a relatively long period.
- Mattresses and pillows: Latex foam is used in producing mattresses and pillows, providing support, comfort, and natural resistance to allergens, mold, and dust mites.
- Adhesives: Latex-based adhesives are used in various applications, including bonding paper, fabrics, and other materials.
- Elastic bands and clothing: Latex is used to produce elastic bands and clothing items such as swim caps, waistbands, and support garments due to its stretchability and ability to retain shape.
- Footwear: Latex is used in shoe soles and insoles for its cushioning, comfort, and shock absorption properties.
- Medical devices: Latex is used in medical devices such as catheters, tourniquets, and airway management devices.
- Sports equipment: Latex is used in resistance bands, exercise balls, and grip-enhancing products.
- Waterproof coatings: Natural latex can create waterproof coatings for various materials, such as fabric, wood, or metal.
- Art and crafts: Latex produces molds, mask-making, and special effects makeup in the film and theater industries.
Global Organic Latex Standard (GOLS) certification ensures natural latex’s organic status and purity. GOLS-certified natural latex can be used in a variety of products, including:
- Mattresses: Natural latex mattresses provide comfort, support, and durability. They are also hypoallergenic and resistant to mold, mildew, and dust mites.
- Mattress toppers: Latex mattress toppers can be added to an existing mattress to provide extra cushioning and support.
- Pillows: Natural latex pillows offer excellent head and neck support, making them a popular choice for allergy sufferers and those with neck or back pain.
- Cushions: Latex foam is used in cushions for seating, such as sofas, chairs, and other furniture.
- Upholstery: Natural latex can produce upholstery foams, which offer excellent durability and comfort.
- Yoga mats: Latex yoga mats provide excellent grip and cushioning, making them a popular choice for yogis.
- Orthopedic products: Natural latex can produce orthopedic supports, such as braces, cervical collars, and joint wraps.
- Pet beds: Latex pet beds provide comfortable, supportive, long-lasting pet sleep surfaces.
- Baby products: Natural latex can be used in baby products, such as crib mattresses and changing pads, due to its hypoallergenic and breathable properties.
- Shoe insoles: Latex insoles provide cushioning and support for various types of footwear.
Remember that for these products to be certified by GOLS, they must meet strict criteria regarding the sourcing and processing natural latex and social and environmental standards throughout the supply chain.
Rubber tree plantation
The rubber tree is tapped by making a small incision. The sap is collected in small bowls. It is then brought to a facility for processing into products like latex foam, balloons, condoms, and medical supplies.
Rubber tree cultivation
Plantation locations
Rubber tree plantations are primarily located in tropical regions, with Southeast Asia being the largest producer of natural rubber. Countries such as Thailand, Indonesia, Malaysia, and Vietnam are known for their expansive rubber tree plantations, which provide a significant portion of the global natural rubber supply. Other rubber-producing countries include India, Sri Lanka, and parts of Africa and South America.
Climate and environmental conditions
Rubber trees thrive in warm, humid climates with well-distributed rainfall. Ideal temperatures for rubber tree growth range between 20°C and 34°C and an annual rainfall of 1500 to 3000 millimeters is necessary for healthy growth. Plantations are typically below 400 meters, as rubber trees become less productive at higher altitudes. Well-drained, loamy soils with a pH of 4.5 to 6.5 are also preferred for optimal growth.
Tapping rubber trees
What is latex made of? Latex refers to the material used to make many latex products, from condoms to mattress foam. Latex is made from the sap of the rubber tree. Here is the method for harvesting the latex from the rubber tree:
Methods and techniques
Tapping rubber trees involves making controlled incisions into the tree’s bark to collect the latex sap. The most common method, the S/2 downward tapping technique, involves making diagonal cuts on the trunk, starting about one meter above the ground and moving downwards. The cuts are made at a shallow angle to avoid damaging the tree and to allow the latex to flow freely into a collection container.
Frequency of tapping
Tapping frequency depends on tree age, size, and environmental conditions. Rubber trees can be tapped once every two to three days. Over-tapping can reduce latex yields and weaken the tree, making it more susceptible to diseases and pests. Tapping usually occurs in the early morning hours when the latex flow is at its highest.
Harvesting and collection
Latex yield
The yield of latex sap varies depending on the age and health of the tree, as well as the tapping method employed. Rubber trees can produce 10 to 30 grams of latex per tapping. The average lifespan of a rubber tree is around 30 years, with peak latex production occurring between the ages of 7 and 18 years.
Factors affecting latex production
Several factors can influence latex production, including climate, soil conditions, tree age, tapping frequency, and tree health. Environmental stressors, such as drought, temperature fluctuations, and disease, can significantly impact latex yield. Proper plantation management, including regular pruning, fertilization, and pest control, is essential to maintain healthy trees and optimize latex production.
Processing raw latex
Here are the steps that describe how latex is made.
Coagulation
Use of acids or other agents
Once the latex sap is collected from the rubber tree plantation, it must undergo coagulation to transform the liquid into a solid. Coagulation involves the addition of acids, such as acetic or formic acid, or other coagulating agents, like ammonium sulfate. These agents cause the latex particles to clump together, separating them from the watery serum.
Formation of latex curds
As the coagulating agents are mixed with the latex, the mixture thickens, forming rubber curds. These curds gradually solidify and are then scooped out from the liquid, creating a solid mass of coagulated rubber that can be further processed.
Pre-processing
Washing and cleaning
The coagulated rubber mass is thoroughly washed to remove impurities, excess coagulating agents, and any remaining serum. The washing process usually involves submerging the rubber mass in large water-filled tanks and agitating it until properly rinsed.
Drying and pressing
After washing, the rubber mass is dried to remove excess moisture. This is typically achieved by pressing the rubber between heavy rollers to squeeze out water and create thin sheets. These sheets are then hung in well-ventilated drying rooms or exposed to the sun for further drying. Once the rubber sheets are completely dry, they are ready for the milling and compounding stage.
Milling and compounding
Mixing with additives
During the milling and compounding stage, the dried rubber sheets are mixed with various additives to achieve specific properties and characteristics required for Dunlop natural latex. These additives may include natural fillers, curing agents, antioxidants, and foaming agents. The mixing process uses specialized machinery, such as internal mixers and two-roll mills, to ensure the even distribution of the additives throughout the rubber mass.
Achieving desired properties
The milling and compounding are critical for creating consistent and high-quality Dunlop natural latex. By carefully controlling the additives and processing conditions, manufacturers can fine-tune the properties of the final latex product, such as its density, firmness, and resilience. This enables producing a wide range of Dunlop latex foam layers suitable for various applications, including GOLS-certified latex mattresses.
Dunlop manufacturing process
The following steps describe how latex foam is made.
Mixing and foaming
Ingredients and proportions
The production of Dunlop natural latex foam begins with the careful formulation of the latex mixture. This mixture contains the milled and compounded rubber and additional ingredients such as water, foaming, and gelling agents. The proportions of these ingredients are crucial to achieving the desired characteristics of the final foam product, including its density, firmness, and resilience.
Mechanical and chemical foaming process
The latex mixture is then subjected to a mechanical and chemical foaming process, which creates a consistent and stable foam structure. This process involves agitating the latex mixture using high-speed mixers or air injectors, causing the formation of countless tiny air bubbles throughout the mixture. Simultaneously, gelling agents are added to promote the stabilization and solidification of the foam structure.
Molding and vulcanization
Pouring latex mixture into molds
Once the foaming process is complete, the latex mixture is poured into large, rectangular molds, which determine the size and shape of the final foam layer. The molds have pins or rods that facilitate heat transfer during the vulcanization process and ensure a consistent foam structure.
Heating and curing process
The filled molds are then placed in a vulcanization oven, and subjected to high temperatures, typically between 100°C and 115°C. This heating process initiates a chemical reaction that cross-links the rubber molecules, creating a strong, elastic, durable foam structure. The vulcanization process typically takes several hours, depending on the desired properties and thickness of the foam layer.
Washing and drying
Removal of residual chemicals
After vulcanization, the Dunlop latex foam layers are removed from the molds and thoroughly washed to eliminate residual chemicals or additives. This step is essential for ensuring the final product is hypoallergenic and free from potentially harmful substances. The washing process involves submerging the foam layers in water and gently agitating them to remove impurities.
Ensuring consistency and quality
Following the washing step, the foam layers are dried in a controlled drying room or through air drying to remove excess moisture. This step is crucial for maintaining the foam’s consistency and ensuring its long-term performance. Once the foam layers are completely dry, they undergo a thorough quality inspection, checking for any defects or inconsistencies before they are integrated into GOLS-certified latex mattresses.
We hope that publishing these steps helped further your understanding of how latex is made.
Companies that manufacture GOLS-certified Dunlop Latex Foam
- Latex Green: Latex Green is a Sri Lankan company that produces GOLS-certified Dunlop latex foam. Their website is: https://www.latexgreen.com/
- Radium Foam (Vita Talalay): Radium Foam is a Netherlands-based company that manufactures Vita Talalay latex foam, which may include GOLS-certified Dunlop latex foam products. Their website is: https://www.vitatalalay.com/
- Cocolatex (Palamuru Diaries Pvt Ltd.): Cocolatex is an Indian company that produces GOLS-certified Dunlop latex foam. Their website is: http://cocolatex.com/
- Arpico (Richard Pieris Natural Foams Ltd.): Arpico, a Sri Lankan company, is known for manufacturing GOLS-certified Dunlop latex foam products. Their website is: https://www.arpicolatexfoam.com/
Quality control and testing
Physical properties
Density and firmness
Manufacturers test the product’s physical properties to ensure the highest Dunlop natural latex foam quality. Density and firmness tests are crucial for assessing the support and comfort provided by the foam layer. Density is measured in kilograms per cubic meter (kg/m³). At the same time, firmness is often assessed using the Indentation Load Deflection (ILD) test, which measures the force required to compress the foam by a specific percentage of its thickness.
Resilience and durability
Resilience and durability tests are conducted to evaluate the foam’s ability to withstand long-term use and maintain its shape and performance. Resilience tests measure the foam’s elasticity and ability to recover its shape after compression. On the other hand, Durability tests simulate the effects of extended use by subjecting the foam to repeated compressions and analyzing its response over time.
Chemical properties
Toxicity and off-gassing
To ensure the safety and health of consumers, manufacturers conduct tests to measure the toxicity and off-gassing potential of Dunlop natural latex foam. These tests involve analyzing the volatile organic compounds (VOCs) emitted by the foam and checking for the presence of any hazardous substances. GOLS-certified latex mattresses must meet stringent requirements regarding VOC emissions and the absence of harmful chemicals.
Allergen and protein content
Another critical quality control aspect is testing the latex foam’s allergen and protein content. While natural latex is known to be hypoallergenic, it may still contain proteins that can cause allergic reactions in some individuals. Manufacturers use specialized testing methods to ensure that the foam’s protein content is below the threshold that can trigger allergies.
Compliance with GOLS certification
Verification of organic materials
To maintain GOLS certification, manufacturers must ensure that the organic content of the latex foam meets the standard’s criteria. This involves verifying the origin of the raw materials and the organic certification of the rubber tree plantations. The verification process also includes regular audits and inspections to ensure compliance with GOLS requirements.
Ethical and sustainable production practices
In addition to verifying the organic content of the materials, GOLS certification also requires manufacturers to adhere to ethical and sustainable production practices. This includes implementing fair labor practices, ensuring safe working conditions, and minimizing the environmental impact of the manufacturing process. Manufacturers must continuously demonstrate their commitment to these principles to maintain their GOLS certification and provide consumers with a truly eco-friendly and socially responsible product.
Integration into GOLS-certified latex mattresses
Mattress Construction
Layers and composition
GOLS-certified latex mattresses feature a unique construction that combines various layers of materials to provide optimum comfort and support. The mattress’s core is typically Dunlop natural latex foam, offering excellent support and pressure relief. Additional layers of Dunlop latex with varying densities and firmness levels can be added to create a customized feel. These layers are often covered by a breathable, organic cotton or wool fabric that enhances the mattress’s comfort and natural appeal.
Customization options
One of the advantages of GOLS-certified latex mattresses is the ability to customize the mattress according to individual preferences. Manufacturers offer various firmness levels, thicknesses, and combinations of Dunlop latex foam layers to suit different sleep styles and body types. Some mattresses even allow for adjustable firmness on each side, catering to the needs of couples with different comfort preferences.
Benefits of Dunlop latex foam layers
Dunlop latex. 2″ or 3″ is available in soft, medium, and firm.
Support and pressure relief
Dunlop latex foam layers are renowned for providing exceptional support and pressure relief. The natural elasticity and responsiveness of Dunlop latex enable it to conform to the body’s contours while maintaining proper spinal alignment. This results in reduced pressure points and improved overall sleep quality.
Breathability and temperature regulation
Dunlop latex foam layers also offer excellent breathability and temperature regulation properties. The open-cell structure of the foam allows for efficient air circulation, which helps dissipate body heat and maintain a comfortable sleeping temperature. This breathability also aids in preventing the growth of mold and mildew, contributing to a healthier sleep environment.
Eco-friendly and hypoallergenic properties
Integrating Dunlop natural latex foam layers in GOLS-certified latex mattresses ensures that the final product is eco-friendly and hypoallergenic. The use of organic, sustainable materials and ethical production practices not only reduces the environmental impact of the mattress but also provides a safe and healthy sleep surface for users. Dunlop latex foam is naturally resistant to dust mites, mold, and mildew, making it an excellent choice for individuals with allergies or sensitivities.
Conclusion
Recap of the Dunlop natural latex manufacturing process
The manufacturing process of Dunlop natural latex begins at the rubber tree plantation, where the latex sap is collected, coagulated, and pre-processed into solid rubber sheets. These sheets are then milled, compounded with additives, and transformed into the foam through a specialized mixing and foaming process. The latex foam is subsequently molded, vulcanized, washed, and dried before undergoing rigorous quality control and testing to ensure its physical and chemical properties meet industry standards. Finally, the Dunlop latex foam layers are integrated into GOLS-certified latex mattresses to create comfortable, supportive, and eco-friendly sleep surfaces.
Importance of GOLS-certified latex mattresses
GOLS-certified latex mattresses represent a commitment to sustainability, ethical production practices, and the well-being of consumers. These mattresses are made using organic materials and adhere to strict guidelines for quality, safety, and environmental impact. By choosing a GOLS-certified latex mattress, consumers can enjoy a comfortable and supportive sleep experience while minimizing their environmental footprint and supporting fair labor practices in the industry.
Frequently Asked Questions FAQ
What are the ingredients in latex?
Latex is a naturally occurring, milky fluid primarily obtained from the rubber tree (Hevea brasiliensis), and it consists of various ingredients. The primary constituents of latex are water (around 55-65%), rubber particles (30-40%), proteins, resins, sugars, and enzymes. In the production of Dunlop natural latex foam, the raw latex is combined with a small number of specific additives to achieve the desired properties of the foam. These additives may include vulcanizing agents such as sulfur, accelerators like zinc oxide or diphenyl guanidine, and foaming agents such as sodium lauryl sulfate or potassium oleate. The raw latex sap, together with the additives, is what latex is made of with regard to the Dunlop process. During the Dunlop process, the mixture is poured into a mold, whipped to create a frothy foam, and then heated to solidify the structure. The end result is a durable, resilient, and supportive foam with natural elasticity, commonly used in mattresses, pillows, and other comfort products.
Is latex made Out of plastic?
No, latex is not made out of plastic. Latex is a natural material derived primarily from the sap of the rubber tree (Hevea brasiliensis). It contains water, rubber particles, proteins, resins, sugars, and enzymes. While latex and plastic may share some properties, such as flexibility and durability, they are distinct materials. Plastics are typically derived from petroleum-based compounds and are made through a polymerization process, whereas latex is a natural substance obtained directly from a plant source.
Some latex products can contain plastic or plastic-derived materials. Although latex is a natural material derived from the rubber tree, it can be combined with synthetic materials, including plastic, to enhance or modify certain properties. For instance, some latex products may have added plasticizers for increased flexibility or be blended with synthetic rubbers or other polymers to improve durability or reduce costs. Such products are often called “blended latex” or “synthetic latex” and may include natural and synthetic materials.
What is natural latex made from?
Natural latex is made from the sap of the rubber tree (Hevea brasiliensis). The sap, called latex, is a milky fluid consisting of water, rubber particles, proteins, resins, sugars, and enzymes. When extracted from the tree, this sap can be processed into various products, such as rubber, foam, and adhesives. Natural latex is different from synthetic latex, created using man-made materials, typically derived from petroleum-based compounds.
What is the main source of latex?
The main latex source is the sap extracted from the rubber tree (Hevea brasiliensis). The top latex-producing countries are mainly located in Southeast Asia, with some countries in Africa and South America contributing to global production. In September 2021, the leading latex-producing countries and their approximate market share were as follows:
- Thailand: Thailand is the largest producer of natural rubber latex, accounting for around 36-37% of global production.
- Indonesia: Indonesia is the second-largest producer, contributing about 25-26% of the world’s latex supply.
- Vietnam: Vietnam ranks third, with around 8-9% of global production.
- India: India contributes approximately 6-7% to worldwide latex production.
- Malaysia: Malaysia accounts for around 4-5% of global latex production.
What are latex gloves made of?
Latex gloves are primarily made from natural latex, which is derived from the sap of the rubber tree (Hevea brasiliensis). The exact composition of latex gloves may vary depending on the manufacturer and the specific formulation used. However, the primary constituents typically include:
- Natural rubber latex: 30-40% of the glove material. This component provides the gloves with elasticity, strength, and barrier properties.
- Water: 55-65% of the glove material. Water is a major component of the latex sap, which is mixed with other ingredients during the glove manufacturing process.
- Proteins, resins, sugars, and enzymes comprise a small percentage of the glove material and are naturally present in the latex sap.
In addition to these primary components, latex gloves may also contain other additives to enhance certain properties, such as:
- Vulcanizing agents: Commonly sulfur, used to cross-link the rubber molecules and improve the strength and elasticity of the gloves. The percentage of sulfur can vary depending on the specific formulation.
- Accelerators: Zinc oxide, thiurams, or carbamates, are used to speed up the vulcanization process. These additives typically make up a small percentage of the glove material.
- Stabilizers and antioxidants: These additives help prevent degradation of the gloves due to exposure to heat, light, or oxygen and typically constitute a small percentage of the glove material.
- Powder or powder-free: Some latex gloves may contain cornstarch powder to make them easier to put on and take off, while others are manufactured without powder to reduce the risk of allergies.
Please note that the exact percentages of these additives in the glove material may vary depending on the manufacturer and the specific formulation used.
Future trends and innovations in the latex mattress industry
As the demand for eco-friendly and sustainable products grows, we expect further innovations and advancements in the latex mattress industry. Manufacturers are likely to focus on developing new materials, processes, and technologies that enhance the performance and sustainability of their products. Some potential areas of innovation include using renewable energy in the production process, developing even more sustainable latex alternatives, and incorporating smart technologies to improve sleep quality and user experience. By embracing these trends and innovations, the latex mattress industry will continue to evolve and provide consumers with increasingly sustainable, comfortable, and high-quality sleep solutions.