Table of Contents
The Arpico latex company is based in Sri Lanka, a country that is renowned for its warm hospitality and 2500 year history.
Arpico produces natural and organic latex foam that comes in various forms.
Organic Latex Blocks
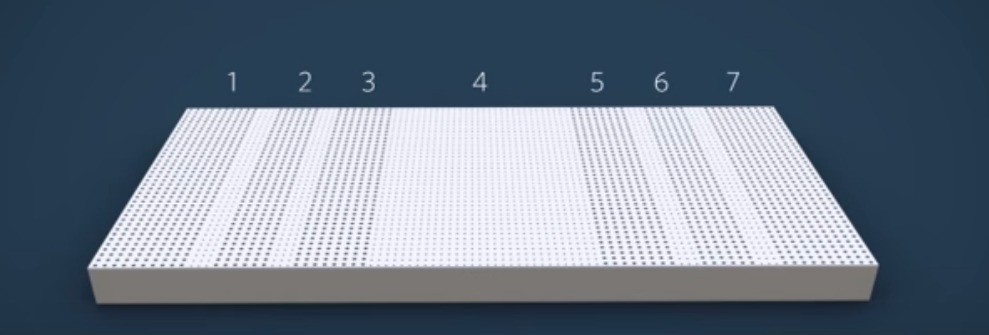
Arpico organic natural latex blocks. These can be moulded with up to seven zones to accommodate for the different pressure relief needs of your hips and shoulders.
Arpico organic natural latex blocks.
These blocks make up the comfort layers of a hybrid or latex core mattress. They are manufactured in different thicknesses and sizes.
Possible variations:
- Thickness
- Size
- Up to 7 Comfort zones: holes of varying diameter are moulded into the foam in order to achieve different firmnesses within the same latex layer.
Continuous Sheets
Arpico continuous natural latex sheets.
Arpico continuous natural latex sheets.
100% natural and organic continuous sheets are produced and shipped in rolls. The sheets can be later cut into shapes for use in a variety of natural latex products.
Pillows
Arpico natural latex pillow variations
100% natural and organic latex pillows are baked into various shapes.
Available shapes:
- Egg crate shape
- Arc shape
- Moulded shape
- Soap bar shape.
Where the latex foam journey starts: the plantation
The latex sap is extracted manually from the rubber tree Hevea Brasiliensiswithout harming it in any way. An angular groove is cut into the side of the tree, intercepting the flow of sap which flows just beneath the bark.
The natural latex sap flows into a coconut shell that is attached to the tree. It is collected by plantation workers every day and sent to the processing plant. It must be collected daily because the natural latex sap coagulates and hardens rapidly.
In some cases, plantations will add vinegar to the latex sap while it is in the coconut shells. This enables the plantation workers to collect the latex in a solid form, which may be more convenient.
Daily Rubber Tree Yield
A rubber tree produces roughly 15 grams of raw latex sap per day. While a rubber tree may live for over a hundred years, it’s economically productive period is roughly 25 years. It takes 7 years for a rubber tree to become mature enough to start producing the milky white latex that is needed to make latex foam.
The rubber tree is not productive year-round, as it goes through a wintering period where it looses all of its leaves. There is less flow of latex sap during this time. As a result, there is less yield in harvest during this time.
During the early stages of growth, the rubber tree is pruned to encourage the growth of a long, straight trunk. After 30 years, when the tree has reached the end of its productive life, it is cut down for lumber. Long and straight trunks can fetch a higher market price.
Natural Latex Foam Is Possible Thanks to Some Ingenious Chemistry
In order to be able to properly mould the raw latex sap into various shapes, it must undergo the process of vulcanization. This is a process in which the raw latex is mixed with sulphur and several other additives and heated. This enables the chain of rubber molecules to cross-link. The sulphur atoms form the link between the rubber molecules.
The technique of vulcanizing latex into rubber was invented by Charles Goodyear in 1839.
The 4 Step Process
The steps involved in turning latex sap into foam are as follows:
- Mixing of the raw latex sap with 5-30% of sulphur (for cross-linking). Other additives are mixed in and each has a separate role in the curing process. Slow vulcanization takes place at the mixing stage. It is necessary to avoid rapid vulcanization during this stage, because it may cause cracks to develop during moulding:
- activator (commonly zinc oxide or stearic acid),
- accelerator (guanidines, thiazoles, dithiocarbamates, xanthates, thiurams),
- ant-foaming agents,
- coagulants (acetic acid, calcium chloride),
- anti-oxidants (amines, phenolics, phosphites),
- anti-tack agents (Rosin derivates, coumarone-indene resins, aliphatic petroleum resins, alkyl-modified phenol-formaldehyde resins).
- colour pigments,
- surfactants,
- softeners (oils),
- Moulding the raw latex and additive mixture. The mixture must be poured into a mould since shaping the mixture after cross-linking has taken place is impossible. The mixture must be shaped prior to heating and curing.
- Heating the raw latex and additive mixture to 250-400ºF (120-200ºC). A higher temperature speeds up the vulcanization process. This results in a fast and complete cross-linking of the latex molecules with the sulphur atoms. Each link is formed by one to seven sulphur atoms. During this process, the density of cross-linking is controlled, which makes for a more flexible and less brittle natural latex foam.
- Washing and drying. The natural latex foam is carefully removed from the mould. It is washed with soap and water and sent on a conveyor that runs it through a series of sprinklers. It is then dried and prepared for inspection.
After this process, the latex foam block is inspected for imperfections.
Pinholes
The latex foam mould has several hundred rods that protrude from it. During the curing process, heat is distributed through the rods. The rods help the latex cure rapidly and evenly. Even vulcanization ( cross-linking of latex and sulphur molecules) makes for more durable natural latex foam.
The mould’s metal rods leave pinholes in the natural latex foam. These pinholes promote ventilation and help keep you comfortable while you sleep. In order to fabricate a zoned latex block of varying firmnesses, rods of diameter are used in the mould and organized into sections.
Cutting the latex foam to shape
The natural latex foam is cut to the customer’s specifications.
The natural latex foam is cut to the customer’s specifications.
The natural latex foam is cut to the customer’s preferences by using specialized industrial cutting blades.
Certification
Arpico natural latex is certified by GOLS and OEK-TEX. The high-quality mattress manufacturer Plush Beds uses GOLS certified Arpico latex foam blocks in their Luxury Bliss, Botanical Bliss and Natural Bliss models.
Shipped Worldwide
From the factory in Sri Lanka, Arpico products are shipped to natural latex mattress manufacturers worldwide. Most latex mattress companies that manufacture mattresses in the USA source materials both locally and globally. Arpico is a latex foam supplier for Plush Beds.